Resistance Welding System
Our Resistance Welding Systems use heat and pressure to create strong, precise welds through electrical resistance. Ideal for industries like automotive and electronics, they offer fast cycles, reduced heat impact, and excellent repeatability for both small and large-scale production.
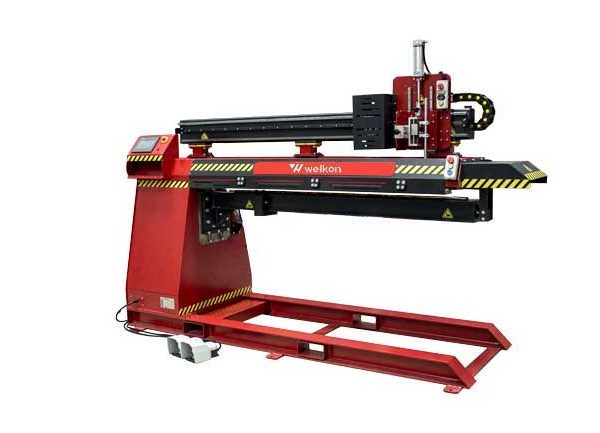
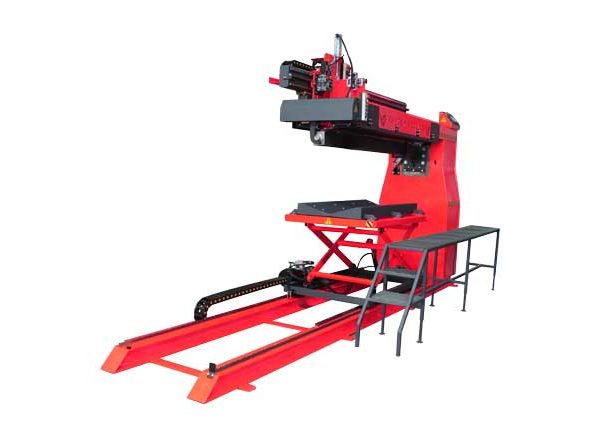

Technical Details of Resistance Welding System
Technical Details | KWBKM-1000 | KWBKM-1500 | KWBKM-2000 | KWBKM-3000 |
---|---|---|---|---|
Work Pieces Diameter (Min.Max/MM) | 100-650 | 150-650 | 250-800 | 350-800 |
Work pieces Lenght (MM) | 1000 | 1500 | 2000 | 3000 |
Metarial Tichkness (MM) | 0,6-10 | 0,6-10 | 0,6-10 | 1-10 |
Pressing Power (BAR) | 8 | 8 | 8 | 8 |
Input Power | 380V-50 Hz | 380V-50 Hz | 380V-50 Hz | 380V-50 Hz |
Welding Speed (MM/Dak) | 0-2000 | 0-2000 | 0-2000 | 0-2000 |
free Speed (MM/Dak) | 3000 | 3000 | 3000 | 3000 |
Dimension (MM) | 2100x2000x1200 | 2700x2100x1200 | 3250x2500x1200 | 4250x2500x1200 |
Color | Red – Black | Red – Black | Red – Black | Red – Black |
Welding Method | Tig /Migmag/Saw | Tig /Migmag/Saw | Tig /Migmag/Saw | Tig /Migmag/Saw |
Weight KG | 1200 | 1600 | 2350 | 3000 |
WHY CHOOSE OUR Resistance welding system ?
Our Resistance Welding System provides efficient, high-quality welds by using heat generated from electrical resistance. It’s ideal for fast, reliable joining of metal parts in various industrial applications.

Resistance Welding System
Resistance Welding Systems are widely used in industrial settings for creating strong, durable welds by applying heat and pressure to workpieces. This process involves passing a controlled electrical current through the materials to be welded, generating heat due to the resistance of the materials to the electrical flow. The heat causes the materials to melt at the contact points, forming a strong bond when pressure is applied.
Common forms of resistance welding include spot welding, seam welding, and projection welding. These systems are typically used for joining metals such as steel, aluminum, and copper, making them ideal for industries like automotive manufacturing, electronics, and appliance production.
Modern resistance welding systems feature advanced control mechanisms, allowing operators to adjust parameters such as current, pressure, and weld time to ensure optimal results. These systems are often integrated into automated production lines for high-volume manufacturing, offering superior precision and consistency in weld quality.
Most Popular Questions for Resistance Welding System
Please check our most popular questions for our welding automation systems that we manufacture, to find answer easily. If you have any further questions, please inform us to get fast and correct answer.
Resistance welding systems offer several benefits, including high speed, efficiency, and low operating costs. Since they do not require filler materials, the process is cost-effective. The systems also provide precise control over welding parameters, resulting in strong, high-quality welds with minimal heat-affected zones, which reduces material distortion.
Resistance welding is primarily used for metals, including steel, stainless steel, aluminum, copper, and their alloys. It is most commonly employed for joining thin metal sheets in industries like automotive, appliance manufacturing, and electronics.
Resistance welding systems are controlled by adjusting key parameters such as welding current, pressure, and welding time. These parameters can be fine-tuned to ensure optimal weld quality, depending on the material, thickness, and specific application. Many modern systems feature automated controls to maintain consistency in high-volume production environments.